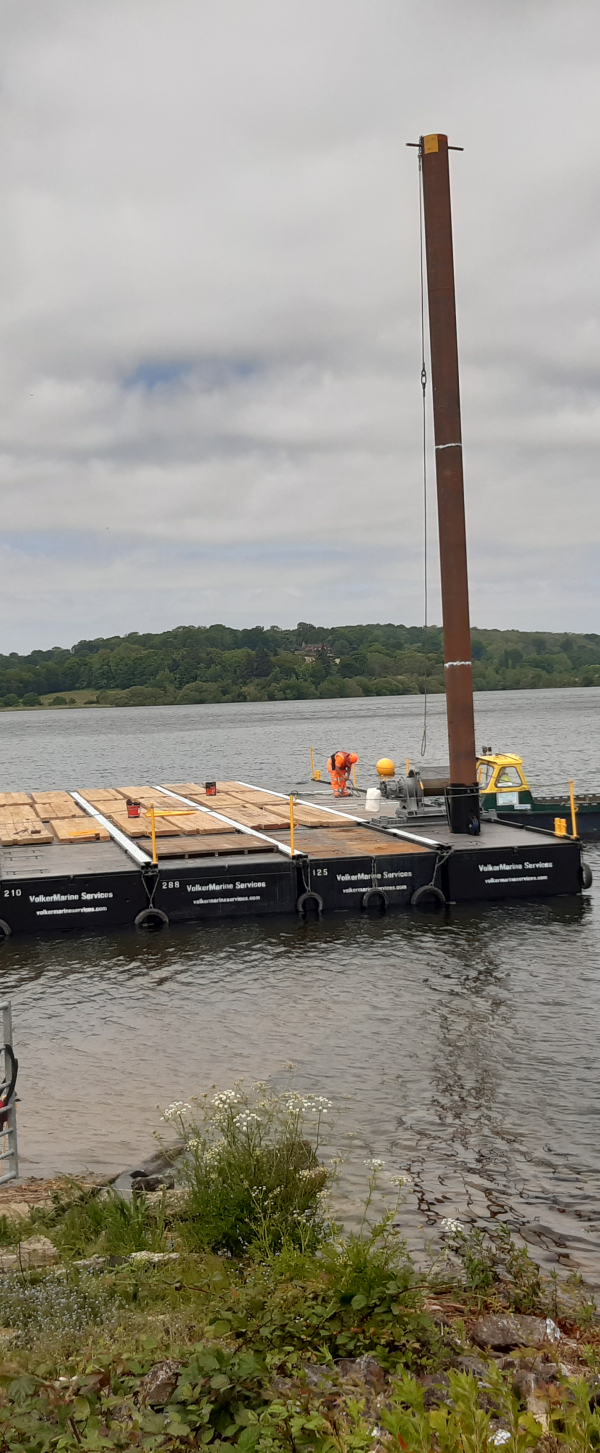
Ardingly Reservoir emergency stabilisation works
During the summer of 2022 extremely low reservoir levels caused slippage along the bank of Ardingly Reservoir, close to Ardingly Activity Centre. This resulted in significant deformation and movement of the retaining wall and the area behind it.
South East Water conducted a survey to find out how floating plant could help facilitate a solution that would provide permanent stabilisation of the area. The survey results found that placing 445, two tonne gravel bags at the toe of the landslide would help reduce the risk of further landslides caused by dropping water levels in the future.
South East Water approached VolkerMarine Services, to not only provide marine plant but to also undertake all emergency stabilisation works. In March 2023, within nine weeks from initial contact with the client the VolkerMarine Services team started work on site.
Due to the sites area of outstanding natural beauty status, the access around the site was very restricted. Access was via narrow, segregated, in and out lanes and weight restrictions were in place, which limited the maximum size of a mobile crane to 90 tonnes. There is a school situated at the entrance to the reservoir, a public car park that needed to remain open for the duration of the works and a number of public footpaths that needed to be diverted.
There were also many environmental constraints to consider and a very strict timeframe to ensure that the activity centre could operate its summer programme.
The initial programme of work would cost £1.1 million, however this was significantly above the client’s budget. This cost was based on the client’s original brief which required the bags to be placed using a six-man dive team working to unhook each bag and verify its placement, this needed to be carried out from floating pontoons. This process could only facilitate 25 bags being placed per day and was estimated to cost £180,000 in labour alone.
VolkerMarine Services developed an alternative proposal, which utilised a quick release hook on a long reach excavator, guided by GPS positioning software. This meant the bags could be positioned below the water at depths of up to 10 metres and the hook released manually by an operative situated on the pontoon, a far quicker and much more precise option.
Placement of the bags below the water level was verified by regular bathymetric surveys, controlled remotely from the shoreline. The outputs from the surveys were key to ensure work was compliant, with only 21 bags (5%) placed more than 0.1 metres away from their specified position and no more than 0.3 metres. Removing the requirement for a dive team increased the number of bags placed per day by 15 to more than 40. This process reduced the working period from 45 to 25 days and removed significant health and safety risks.
To facilitate these works, VolkerMarine Services mobilised a main pontoon platform consisting of 20 Linkflote pontoons, on to which a 35 tonne long reach excavator was tracked. The main pontoon was then held in position by spud legs to minimise the movement of the pontoon along the toe of the slip.
The main pontoon was supported by two supply pontoons, each consisting of six Linkflote pontoons that were being continuously loaded with up to 18, two tonne gravel bags. The supply pontoons were then moored alongside the main pontoon to ensure it had a continual supply of bags to place.
Adopting this digital construction methodology, removed health and safety risks to the dive team and transformed the project’s overall scope. A total cost reduction of £522,000 was saved on combined plant, labour and overhead costs, this halved the original estimated cost.
The work was completed ahead of schedule, within an already tight timeframe, whilst also preventing further damage to the area.