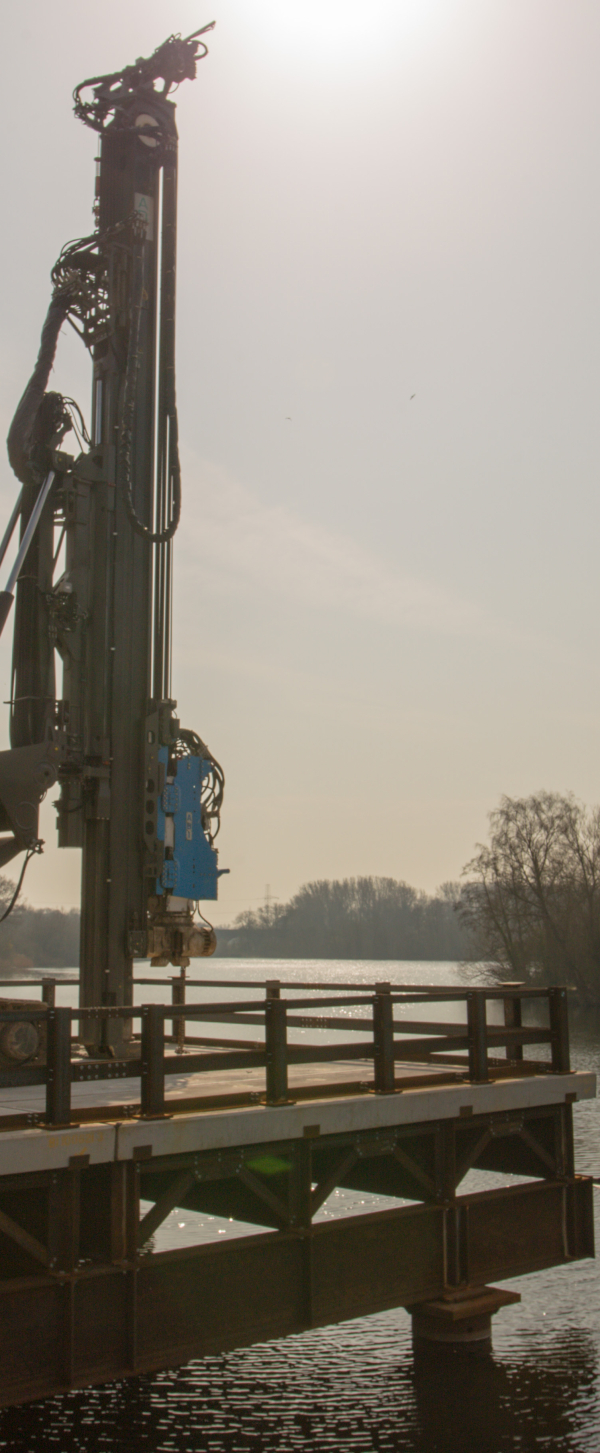
HS2 Colne Valley Viaduct Cofferdams
In April 2021 VolkerGround Engineering embarked on its largest project to date, the cofferdams required for the construction of the Colne Valley Viaduct, on behalf of VolkerStevin, who were working with the main works civils contractor Align, a JV comprising Bouygues, VolkerFitzpatrick and Sir Robert McAlpine. These works were part of the Central 1 section of HS2 Phase One that Align is delivering. This includes a viaduct which will carry the high speed railway across a series of lakes and waterways on the north west outskirts of London.
The viaduct will be almost a kilometre longer than the Forth Rail Bridge. In order to deliver the scope of works, VolkerGround Engineering utilised a wide range of installation techniques that included our ABI TM22 leader rig, movax and conventional piling where they were required to work over water. The team constructed 39 land based cofferdams and 17 from the jetties established over the lakes to support the construction process, and enable the construction of the viaduct foundations.
As the Colne Valley area is environmentally sensitive, a number of locations required sealant in the sheet pile clutches. This provided a water-resistant structure, restricting any seepage from the concrete into the surrounding watercourse from the rotary bored piles installed within the cofferdams.
The team overcame many challenges delivering this project. Due to the vast number of materials and size of the scheme spanning over 3km, they used a single point of access to reduce the impact on the local infrastructure.
This required continuous liaison with transport companies, HS2 Ltd and the on-site Align logistics team. VolkerGround Engineering carefully coordinated material procurement, delivery and handling with the client and other trades on site to determine what other movements were planned, thereby preventing clashes.
Working from man-made jetties with strict design tolerances, VolkerGround Engineering programmed the sequence to ensure that the crane would always work ahead of the rig to maintain proximity tolerances. The team managed multi sequence changes for the installation of the cofferdams by adopting a flexible approach to sectional availability.
With a true collaborative approach, VolkerGround Engineering worked with VolkerStevin and Align as one team in a shared office, to facilitate immediate resolution of issues and early mitigation of any risks to programme and cost. This open and honest approach also enabled full transparency and sharing of information, developing a strong bond of trust between the teams. Whenever the opportunity arose, VolkerGround Engineering also shared labour and plant resources, thus reducing costs for all parties.
Weekly and ad hoc meetings enabled open lines of communication, which assisted with crucial forward planning allowing VolkerGround Engineering to deliver the right solution with certainty.
The high standards of Health and Safety achieved by VolkerGround Engineering, is testament to the dedication of the whole team caring about their own personal safety and the safety of those around them.
The team successfully delivered the programme ahead of schedule, and within budget.