VolkerTrenchless Solutions develops innovative technique
VolkerTrenchless Solutions (VTS) recently completed a challenging Horizontal Directional Drilling (HDD) project for the Anglian Water Strategic Pipeline Alliance in the East of England. The project faced significant challenges, including fractured chalk beneath critical infrastructure and logistical hurdles, yet through innovative techniques our team delivered impressive results ahead of schedule.
Project Overview
VTS worked closely with Anglian Water over four years from the initial early contractor involvement (ECI) phase through to delivery, installing over 11km of pipeline. One particular crossing presented a significant number of challenges for the team. The Kennet crossing involved drilling a 775m HDD bore beneath a Network Rail asset, the A14 dual carriageway, and the B1506 road. The installation was designed to place a 710mm PE 100 SDR11 pipe at a depth of 13.3m under the railway and 13.8m under the A14. Compounding the technical complexity was the fractured chalk ground formation, a known risk that had caused delays and additional costs on similar crossings in the region.
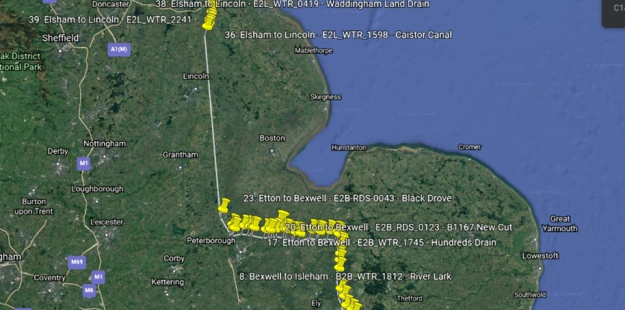
Drill locations
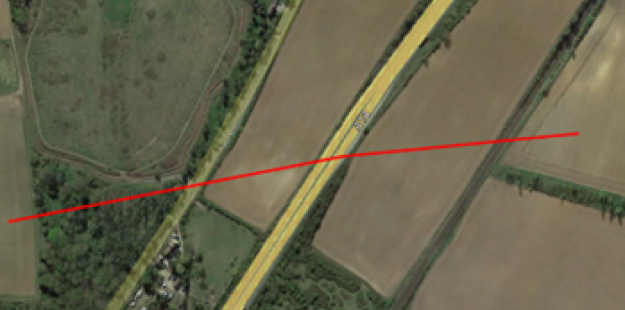
The crossing under a Network Rail asset, the A14 dual carriageway, and the B1506 road
Challenges
Ground investigations revealed fractured or structureless chalk at the site, which posed a risk of frac-outs, where drilling fluid escapes to the surface through ground fractures. Using detailed hydrofracture analysis and mud pressure calculations the team assessed how the ground would react to pressurised drilling fluids. Our analysis provided essential data on the likelihood of existing fractures opening further during the drilling process, which guided decisions on managing downhole pressures to prevent frac-outs.
Further logistical complications arose due to local bridge weight restrictions. The original plan for fluid management involved over 230 tanker movements to transport drilling fluids between the pipe side and rig side. However, two local bridges had 3-ton weight limits, requiring a 9-mile detour for each tanker which would have resulted in an extra 1,526 miles of travel and 3,510 kg of CO2 emissions.
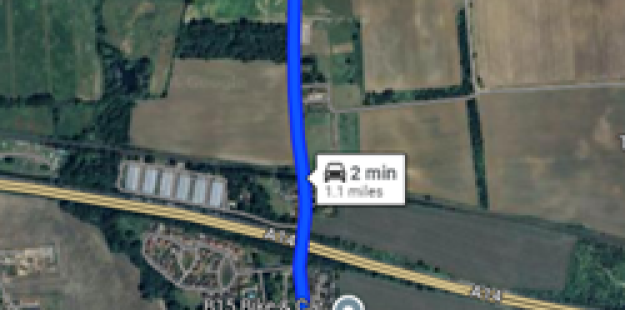
Kennet travel distance
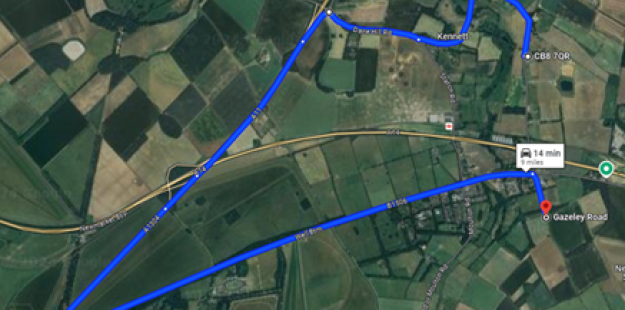
Tanker travel distance
Innovative Solutions
VTS implemented several innovative measures to overcome these challenges, central to which was the use of an intersect HDD methodology. In this approach, two rigs drilled from opposite ends of the bore path, meeting in the middle to complete the pilot bore. One rig was equipped with a magnetic source on its bottom hole assembly which allowed the other rig to determine the exact distance and direction for a precise intersect. This method minimised downhole pressures, significantly reducing the risk of frac-outs.
In addition, VTS introduced two advanced pieces of equipment that proved pivotal in reducing costs and environmental impact, including an innovative tooling assembly developed by VTS which has not been previously adopted by the HDD industry. Bringing technologies from the vertical drilling sector, developed primarily for offshore oil and gas exploration, the team were able to connect the drill strings to allow drilling fluid to be pumped and recirculated by both rigs during the rearming phase:
- Downhole Swivel Assembly: The team utilised a swivel master, a drill pipe tool which enabled the pipe-side rig to act as a support rig, providing tension on the drill string and allowing both rigs to apply rotational force. This resulted in a dramatic reduction in rotational friction. With its hollow interior, the swivel also facilitated fluid passage between the rigs, enabling the continuous recirculation of drilling fluid.
- Float Valves: These valves are located within a crossover and prevented drilling fluid from leaking during reaming phases, allowing fluid to be pumped between the rigs rather than relying on tanker movements.
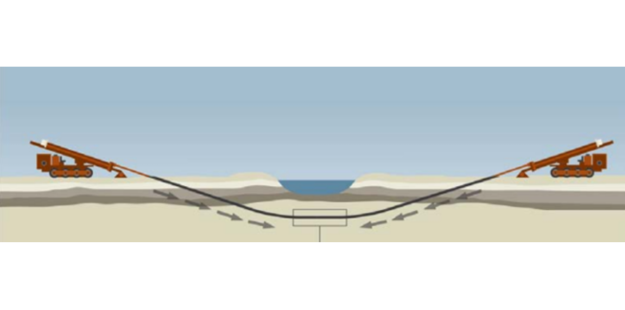
Intersect Sketch
Conclusion
VTS’ innovative approach at the Kennet HDD crossing showcases our commitment to sustainability and efficiency. By adapting techniques from the oil and gas sector and implementing advanced fluid and pressure control, VTS not only completed the project two days ahead of schedule but also reduced its environmental footprint as well as achieving significant carbon and cost savings against the target price. This success sets a new standard for trenchless engineering, particularly in complex geological conditions, and positions VTS as a leader in innovative, sustainable infrastructure solutions.